
Turboprop Question
Moderators: Guru's, The Ministry
Turboprop Question
On aircraft such as The Viscount,Vanguard 748 etc,the instructions are not to adjust the props but only to use the the throttles.Is this due to a limitation in FS or does it reflect the real aircraft? I believe aircraft such as the Dash8 have prop conditioning levers.Are these a more recent development?Thanks gents
EricT

Now at the age where I know I like girls but can't remember why!
Re: Turboprop Question
Hi Eric,
I bookmarked this from pprune as it explains things pretty well... Here's a hands-on example of how to operate turboprop controls that I posted a while ago in reply to a similar question. Can't find the original post since the search functions are out, out and out.
I bookmarked this from pprune as it explains things pretty well... Here's a hands-on example of how to operate turboprop controls that I posted a while ago in reply to a similar question. Can't find the original post since the search functions are out, out and out.
Basic operation
You have two levers for each engine, Power Lever (PL) and Condition Lever (CL).
The range of the CL is divided into
- Fuel off where the engine goes to feather (83.5 degrees pitch) and the fuel is cut off
- Start, where you are supplying fuel to the engine but the prop is still feathered
- UNF, UNFeathered, where the prop is out of feathered and basically in constant speed mode trying to maintain 1180 RPM but without the bottoming governor (more on that later)
- Min to max constant speed (CS) range where the prop RPM is controlled to be within 1180 RPM (min) and 1384 RPM (max).
- T/M (torque motor) lockout which will lockout the engine control unit (ECU, or digital ECU, DECU, in B model a/c) if it malfunctions. Once T/M lockout is activated, you have to shut down the engine (put the CL in fuel off) to reactivate it.
The power lever range goes from full reverse through ground idle (GI) to flight idle (FI) and then on up to full power. Below FI you are operating in the beta range where the PL position (unless the CL is in feather or you feather manually) directly controls the prop pitch from -16.5 to +10 degrees. Above FI there is a minimum pitch stop ranging from +10 (FI) to +25 (full power) degrees pitch.
As you go from PL full aft to PL full forward, more and more fuel is added to the engine (naturally) through signals to the Hydro-Mechanical Unit (HMU). At low power settings (below approx 30%), this amount of fuel is not enough to spin the propeller up to the commanded 1180 RPM at the pitch setting commanded by PL in beta range or at the minimum pitch stop.
Why do we have a beta range? Due to the slow response to throttle setting changes in turbo engines it is very impractical to use the throttle to control movement on the ground. You would have to wait for the gas generator to spin up (Ng increase), providing more torque through the power turbine (PT) increasing the prop RPM (Np). The prop CS governor would then tell the pitch control unit (PCU) to increase the prop pitch and then you would get additional power. In beta mode, you change the pitch first instead using the inertia in the propeller system to provide thrust, letting the Ng accelerate or decelerate in response to Np to keep Np constant.
If the amount of fuel burned below 30% won’t keep the prop spinning at 1180 RPM, what keeps it at constant speed in the beta range? This is where the previously mentioned bottoming governor (BG) comes into play. The BG is active when the CL is above UNF and will send a signal to the HMU to add fuel above what the PL setting is dictating to keep the Ng up. The normal reference Np for the BG is 1040 RPM but to give more power in full reverse the BG reference will change to 1200 RPM Np when the pitch goes below –10 degrees (<-10 on both engines on older versions).
CTOT
Early on it was discovered that the torque set in the beginning of the take-off roll would increase as the ram air effect increased with airspeed. To avoid having to stare at the torque (Nq) reading during the entire takeoff roll, decreasing the PL setting to keep it at 100% and not above a CTOT (Constant Torque on Take-OFF) system was added. When active, this system will signal to the HMU through the ECU to add fuel until the preset Nq is reached as soon as you set the PL above a certain position.
AC
If an engine dies there’s an autocoarsen (AC) system which will detect this. It then proceeds to feather the dead engine automatically. There’s an inbuilt safetguard making it impossible to feather both engines in flight should this system fail. In short, the feathering signal to the right prop control unit pulls a relay cutting off the feathering signal to the left. The AC system continues to monitor a failed engine and will bring it out of AC mode should the engine parameters used to detect a flameout increase above the threshold values again (although in reality, the conditions are such that the system will probably latch until action is taken).
APR
340B a/c has something called automatic power reserve (APR) which when one engine goes into AC during CTOT operation automatically adds 7 percent units of torque to the other engine to compensate for the loss of thrust.
Cheers,
/ft
Ben.
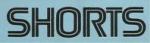
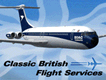


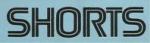
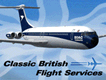

- Motormouse
- Concorde
- Posts: 1343
- Joined: 09 Sep 2004, 22:03
- Location: In a Hangar
Re: Turboprop Question
In simple terms, if we accept that max power must = max load then it must follow that we need to also govern
The prop load and speed to avoid overloading. The system component that does this is called a propellor governor.
Because the types of engines , Dart, use a propellor which is directly driven , the prop governor can be linked with the
Fuel control mechanism, so we only get 1 lever for Biggles to use.
The Dash 8, PW120 series engine has a free power turbine, so prop and gas generator sections of the engine are controlled separately, ergo, Biggles has 2 levers to play with on each engine.
Fs is programmed for the latter type of engine, and has to be fooled by gauge to respond properly as the former type of engine.
Ttfn
Pete
The prop load and speed to avoid overloading. The system component that does this is called a propellor governor.
Because the types of engines , Dart, use a propellor which is directly driven , the prop governor can be linked with the
Fuel control mechanism, so we only get 1 lever for Biggles to use.
The Dash 8, PW120 series engine has a free power turbine, so prop and gas generator sections of the engine are controlled separately, ergo, Biggles has 2 levers to play with on each engine.
Fs is programmed for the latter type of engine, and has to be fooled by gauge to respond properly as the former type of engine.
Ttfn
Pete
An Elephant is a Mouse designed to
a government specification.
a government specification.
Re: Turboprop Question
Thanks for the replies.I'll have to read them a few times to grasp the concept!
EricT

Now at the age where I know I like girls but can't remember why!
Re: Turboprop Question
I would add a 3rd type, the constant speed, single shaft engine such as the Allison T-56/501 series and I think, some of the Garretts. The RR Dart series varies the power and RPM with the power lever (throttle and fuel trimmers). The Allison maintains a constant, fixed RPM for all flight conditions and varies only the power. With this plan, there is little, if any, lag in acceleration time.
For the Allison, in the flight range, the prop (and engine) is always operating at fixed, constant RPM, (about 1050 for the prop, 13600 for the engine) with no RPM control allowed to the pilot. The prop, is in effect, a very large speed governor. The condition levers have only four positions: feather, stop, run and airstart. The power lever controls the engine temp/fuel flow, much as a thermostat. Turn up the temp, power increases, prop takes a bigger cut to maintain RPM. Turn down the temp, prop flattens to maintain RPM and prevent a flame out. This all applies only to the flight range.
The ground range/beta, also controlled by the power lever, is another story, with some very limited control over RPM, but I won't go into that here.
Hope this adds a little more confusion to the pot!
Hy
For the Allison, in the flight range, the prop (and engine) is always operating at fixed, constant RPM, (about 1050 for the prop, 13600 for the engine) with no RPM control allowed to the pilot. The prop, is in effect, a very large speed governor. The condition levers have only four positions: feather, stop, run and airstart. The power lever controls the engine temp/fuel flow, much as a thermostat. Turn up the temp, power increases, prop takes a bigger cut to maintain RPM. Turn down the temp, prop flattens to maintain RPM and prevent a flame out. This all applies only to the flight range.
The ground range/beta, also controlled by the power lever, is another story, with some very limited control over RPM, but I won't go into that here.
Hope this adds a little more confusion to the pot!
Hy
- Motormouse
- Concorde
- Posts: 1343
- Joined: 09 Sep 2004, 22:03
- Location: In a Hangar
Re: Turboprop Question
Lol! And there I was trying not to confuse the poor chap too much.
Incidentally, the turboprop aeroplanes I hold type ratings for have following powerplants,
PT6, Tpe331, PW120, PW123 and Dart.
Not to mention the Allison in the Herk when I worked for Betty Windsor Airways.
The Dart uses a cunning contraption in its engine controls called a mixing box, to achieve single lever control of two
Components, governor and fuel control. An absolute pig to set up, easy to get wrong, and most leave well alone if its working right!
Incidentally, the turboprop aeroplanes I hold type ratings for have following powerplants,
PT6, Tpe331, PW120, PW123 and Dart.
Not to mention the Allison in the Herk when I worked for Betty Windsor Airways.
The Dart uses a cunning contraption in its engine controls called a mixing box, to achieve single lever control of two
Components, governor and fuel control. An absolute pig to set up, easy to get wrong, and most leave well alone if its working right!
An Elephant is a Mouse designed to
a government specification.
a government specification.